Kleemann showcases its new mobile cone crusher MCO 9 EVO at Intermat
Kleemann showcases its new mobile cone crusher MCO 9 EVO at Intermat
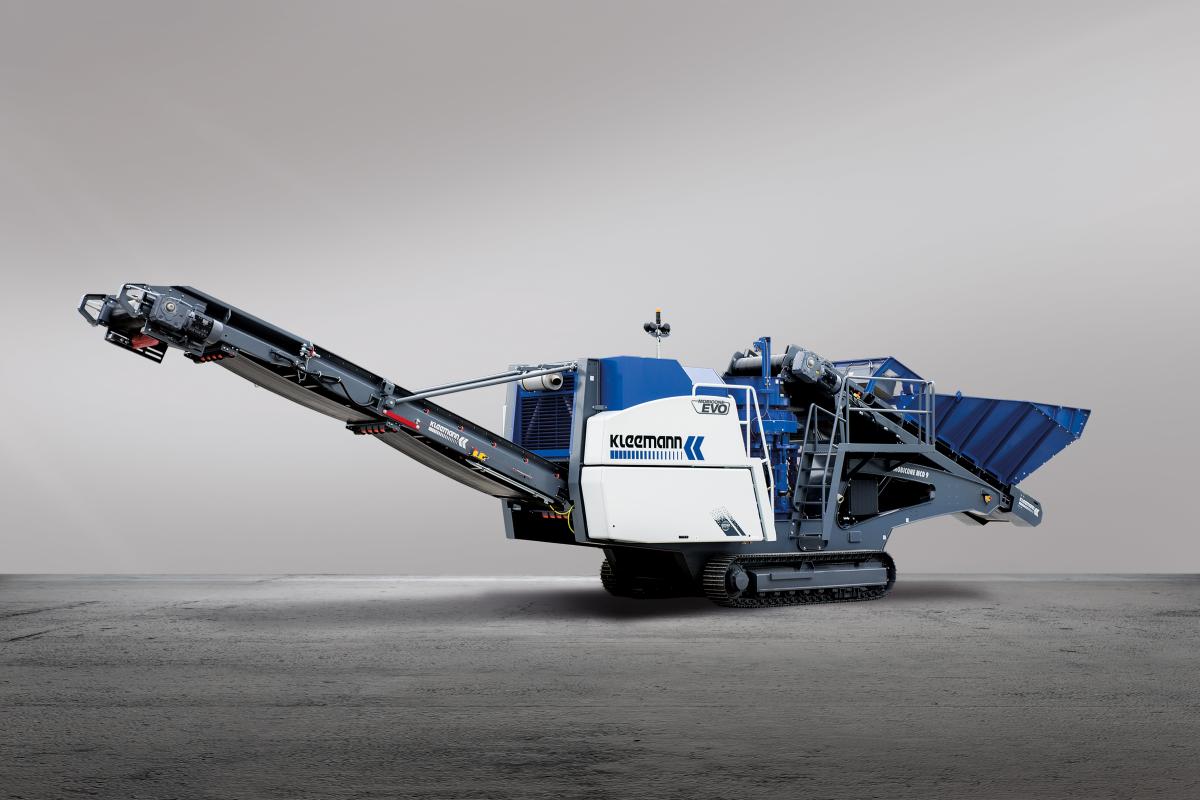
Kleemann exhibits its new mobile cone crusher Mobicone MCO 9 EVO for the first time also in France at the stand of Wirtgen France. The mobile jaw crusher Mobicat MC 110 Z EVO is also on show in Paris.
The mobile cone crusher closes one of the final gaps in the Kleemann model range. The MOBICONE MCO 9 EVO is compatible with the mobile jaw crusher MOBICAT MC 110 EVO, which is also on display at the trade fair.
Powerful, efficient and easy to transport: Kleemann MCO 9 EVO
Similar to other Kleemann crushers in the EVO line, the MCO 9 has been developed especially for the needs of customers in the contractor market. The drive concept with a crusher direct drive, as well as electric drives for the conveyor belts, promises very efficient operation like the other Kleemann EVO models. And the new plant also does not lack in power, quite the contrary: The 248 kW of the drive unit is optimally used thanks to a performance-enhanced crusher housing design. A continuous drive power at the crusher of 160 kW is available. Together with its large stroke, the cone crusher enables not only crushing capacities of up to 260 t/h, but also achieves a higher crushing ratio and produces a final product with a higher amount of fine particles in comparison to other cone crushers in this class. In addition, the crusher is optionally equipped with an anti-spin system, which prevents the crusher cone from rotating, thus significantly reducing the wear in this area. A magnet and a metal detector are also available as options, which further increase the operational safety.
Simple transportation, clear operation
Weighing approx. 30 tons, the MCO 9 EVO is very easy to transport and is ready for operation again quickly and simply in just a few steps. The feeding unit can be shifted by a simple slide mechanism from the transport to the operation position. This slide mechanism enables adjustment of the material discharge pattern to the crusher during operation. For instance, the feeding unit can always be optimally adapted to the crushing product, thus preventing wear on one side. For the operating concept Kleemann has focussed on the reliable touch panel control system, which has already been tried and tested in the other EVO plants. This control system impresses on account of its transparency and intuitive design. Operators who already have experience with other EVO plants therefore won't take long getting used to this control system.
Optimal linkage options
The operation of the plant in conjunction with a mobile jaw crusher of type Mobicat MC 110 Z EVO, which possesses the same drive concept, results in the best possibilities of electrical locking. An ideal material flow is always top priority with a linked plant combination. The MCO 9 and the MC 110 offer the best preconditions for this purpose. Both plants are equipped with a so-called "Continuous Feed System" (CFS), which individually controls the material flow of each plant. If the control systems of the plants are connected, both CFS exchange information with each other. In simple terms, this means that the MCO 9 controls not only its own conveyor unit via its crusher filling level, but also the conveyor elements of the upstream MC 110. For instance, the jaw crusher in the first crushing stage always provides the exact amount of material so that the cone crusher constantly maintains its set filling level, thus achieving optimal efficiency.
MOBICAT MC 110 Z with effective preliminary screening
The MC 110 Z also impresses with its well-known effective double-deck grizzly, which not only enhances the overall performance of the crusher, but also the quality of the final product. The side discharge conveyor of the grizzly remains at the machine for transportation, which also contributes to the good transport characteristics, like the hydraulically operated hopper walls of the feeding unit. The crusher unit impresses with its raised crusher jaw, which avoids blockages in the crusher area and significantly improves the material feed characteristics. With the optional crusher deblocking system the crusher drive can also be reversed if required, meaning blockages in the crushing jaw can be removed quickly and simply. Similar to the MCO 9, the drive concept with a crusher direct drive also provides very efficient consumption values. In operation the mobile plant combination of the two machines leads to a very productive and, at the same time, very economical result.
Image,video ©: Kleemann