ContiTech develops world’s first polyamide strut mount for passenger car chassis
ContiTech develops world’s first polyamide strut mount for passenger car chassis
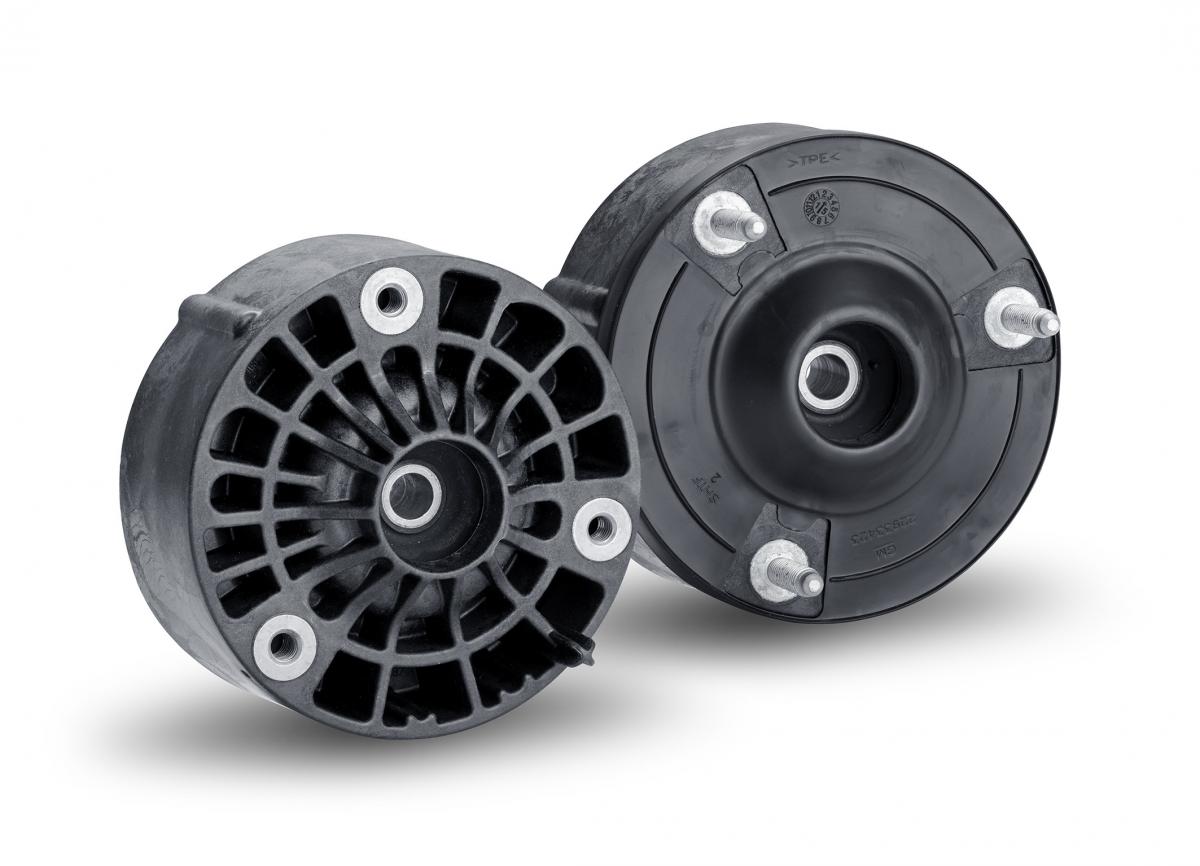
Lightweight variant with fiberglass-reinforced polyamide 25 percent lighter than aluminum design
ContiTech Vibration Control – the strut mount specialist based in Hanover in Germany – has developed a strut mount in which fiberglass-reinforced BASF Ultramid polyamide is also used as the primary structural component. It is the first strut mount made of this material, which is used both at the front and rear axle in the chassis environment of passenger cars. The strut mount offers significant advantages over traditional variants made from steel or aluminum: a weight reduction of around 25 percent and a longer service life. At the same time, a highly insulating rubber element enhances ride comfort. In collaboration with General Motors LLC, ContiTech developed the strut mount for the new Cadillac CT6, which is set to be launched on the market at the end of 2015.
“High-performance plastics are the material of the future in the automotive industry,” says Kai Frühauf, who heads ContiTech Vibration Control. “Thanks to our many years of experience and extensive materials expertise, we are among the top partners when it comes to innovative new developments with this material. This strut mount designed for passenger car bodies represents another step forward.”
Enhanced Safety, Even Under Extreme Stress
In passenger cars, the spring strut mount is the interface between the spring strut and body. It enables precise and low-friction rotational movement of the spring strut in the front of the vehicle, thereby ensuring optimum contact of the tire to the road. The vehicle is easier to steer.
As a chassis component, it is subjected to extreme stress. Spray water, road salt, sand, gravel, and vibrations can cause the spring strut to wear. If it is no longer fully functional, the shock absorbers – among other things – are more highly stressed. Vibrations and noise from the axles are more pronounced, resulting in reduced ride comfort.
The new two-section, three-path bearing from ContiTech comprises both fiberglass-reinforced polyamide and aluminum components. This brand-new design can even withstand shock loading as high as 75 kN, equivalent to driving a car along a badly potholed road. The strut mount also ensures that only minimal countertorque acts on the shock absorber. This component too is subjected to less stress which, in turn, enhances safety in the vehicle.
The new strut mount from ContiTech also enhances ride comfort. This highly durable, extremely comfortable, and innovative strut mount was developed in close cooperation with the customer. “Key to success was the early integration of our customer in the development process, which meant that we were involved in system design right from the outset and could contribute our specialist experience,” reports Stefan Wöhler, a developer at ContiTech Vibration Control.
ContiTech Vibration Control has been developing light weight products, using BASF Ultramid material, for the automotive industry since 2006. Product solutions include heavy-duty engine mounts, with the annual production volume in 2013 exceeding three million. In 2009 ContiTech Vibration Control also launched a lightweight transmission crossmember from the lightweight material to support the forces and torques of the engine transmission unit. The weight is 50 percent less compared to an aluminum component. In 2014, ContiTech presented the first rear axle transmission crossmember made from this high-performance polyamide. ContiTech has already delivered millions of torque rod supports and torque reaction mounts made from polyamide.
Image,video ©: Continental